-
Gun Proof in India - An Historical Account
With all of the recent attention being paid on these forums to the Lee Enfield and proof pressures, I thought the following extract would be of value to some of you - I certainly don't want it to start another ruckus 
I have an awful lot of reference material and while reading today I came across a paper titled "Gun Proof in India - An Historical Account." It was written by Mr. A. G. Harrison the former Proof Master at the Rifle Factory Proof House, Ishapore, India and was published in "The Gun Digest, 33rd Edition, 1979."
I'll get it scanned later but for now I've extracted the part that interested me:
From 1908 to 1950 all military bolt action rifles made at Ishapore were proof tested with a dry proof round followed by an oiled proof round. The proof cartridge was loaded to 24 tons (2240lbs = 1 ton) psi breech presure, or 25% higher than the service pressure.
In 1950 the material for rifle bodies (they made No.1 Mark 3* rifles; my addition) was altered from an EN steel to SWES 48 steel (not heat treated) except for the recoil shoulder and cam recess in the receiver. With this change the rifle receivers distorted when oiled proof cartridges were fired. This was discovered when hard and sometimes impossible bolt retraction was experienced. Large quantities of rifles were rejected. To avoid rejections the authorities ordered discontinuance of the oiled proof. Therefore from 1950 to the end of SMLE rifle production (June 1965) rifles made at Ishapore were proof tested with one dry proof only, although the specification called for both dry and oiled proof.
A bolt action rifle similar to the SMLE Mk. III*, modified to fire the 7.62 NATO cartridge was produced at Ishapore, first in February 1965. Their receivers were made of SWES 48 steel, un-heat-treated, and with the NATO proof cartridge receivers were found to distort with the oiled or the dry proof round! The material was changed to an EN steel so now the rifles stand up better to dry and oiled proof.
There's a lot you can read into what the author has said but I am not going to make any assumptions.
Information
|
Warning: This is a relatively older thread This discussion is older than 360 days. Some information contained in it may no longer be current. |
|
Last edited by Amatikulu; 06-27-2009 at 08:23 PM.
-
The Following 3 Members Say Thank You to Amatikulu For This Useful Post:
-
06-27-2009 08:06 PM
# ADS
Friends and Sponsors
-
FREE MEMBER
NO Posting or PM's Allowed
There's a lot you can read into what the author has said
I'll drink to that, for sure.
-
-
That's intersting Amat. Like I said, we tested the rifle body steel from Indian 7.62 AND .303" SMLE's and contrary to popular belief, they were all the same...., within the realities/peramaters of steel mixing of course.
-
-
FREE MEMBER
NO Posting or PM's Allowed
Me .... I think I´ll keep my 7.62 chamber (very) dry in future. When I recently got the rifle, rounds would not fall into the chamber of their own weight and were sticky extracting. Sent the action to Germany
´s leading gunsmith (head of the German guild of gunsmiths and maker of gunsmith tools, mainly reamers). He inspected the chamber and tested head space. Told me that headspace was not up to German commercial standards, but well within limits.The chamber was re-reamed in the shoulder area and is now spot on and I now only have to neck size. I didn´t like the alternative advice given by my re-loading expert who advised the use of a special (smaller) die, made for full auto and machine guns. So, is there a difference in size between 7.62 full auto cases and commercial?
-
Peter, the way I read what Mr. Harrison published, the Mark 3* up to 1950 and the 2A/2A1 rifles from 1965(apart from inital 1965 production) were made with EN grade steels - confirming exactly what you found in practice.
There was once a theory circulating that the 2A/2A1 rifles were made from a different steel to allow the use of 7.62 NATO ammunition. It would seem that was not the case. The explanation is that from 1950 to 1965, Ishapore made receivers for the Mark 3* in a different steel grade. Due to the dropping of the oil proof during this period, it is obvious that it was not as strong as the EN grade of steel. SWES 48 was only just strong enough to allow dry 303 proof and was not at all suitale for 7.62 NATO proof (dry or oiled).
-
-
Banned

Originally Posted by
villiers
Me .... I think I´ll keep my 7.62 chamber (very) dry in future. When I recently got the rifle, rounds would not fall into the chamber of their own weight and were sticky extracting. Sent the action to
Germany
´s leading gunsmith (head of the German guild of gunsmiths and maker of gunsmith tools, mainly reamers). He inspected the chamber and tested head space. Told me that headspace was not up to German commercial standards, but well within limits.The chamber was re-reamed in the shoulder area and is now spot on and I now only have to neck size. I didn´t like the alternative advice given by my re-loading expert who advised the use of a special (smaller) die, made for full auto and machine guns. So, is there a difference in size between 7.62 full auto cases and commercial?
Villiers
Here in central Pennsylvania the Remington 760 pump action is very popular for hunting in the woods where fast follow up shots are needed at running deer. Several people I hunted with were given the same advice as you were and they used small base reloading dies and all of them suffered the same problem, premature case head separations from over sizing the cases. If anything the 760 has a larger diameter chamber and longer headspace, I always used a full length die set to only partial resize my cases and never had any case head separations.
The bottom line was I never owned a rifle that needed small base dies, American made cases are on the small side on base diameter anyway.
RCBS Reloading die FAQ
Q. I see a Small Base Die Set listed for my caliber. Do I need these or should I buy a Full Length Die Set or Neck Die Set? How does each set differ?
A. The Small Base Die set is intended for use for ammunition to be used in auto, semi-auto, and lever action rifles so that the loaded round chambers and extracts easily. The Small Base Sizer Die sizes the case from the shoulder to the head of the case a couple of thousandths smaller than a Full Length Sizer Die. In certain calibers it also sets the shoulder of the case back a thousandth or two more than the Full Length Sizer Die. The Full Length Die Set or Neck Die Set is not normally recommended for ammo to be used in auto, semi-auto, or lever action rifles. The Full Length Die set is recommended for ammunition used in bolt action rifles, particularly for ammunition to be used for hunting. The Neck Die Set can also be used to produce ammunition for use in bolt action rifles. The Neck Sizer Die sizes only the neck of the case so it will hold the bullet firmly. It does not size the body of the case nor does it set the shoulder back. Neck sized cases will usually chamber for three or more firings, depending on the powder charge and chamber dimensions. However, over a period of time, a slight drag will be noticed when the bolt is locked. At this point, cases will need to be full length sized and the shoulder set back so they will chamber and extract easily.
In my 760 pump I could neck size the cases twice and the cases would eject correctly BUT on the third firing I would have to wait for the case to cool for 5-10 seconds before they would eject. For hunting all cases were full length resized and for range practice headspace control shims or washers were used under the die lock ring to partially resize the case.
-
FREE MEMBER
NO Posting or PM's Allowed
Ed, I use a f/l RCBS die for my 7600 in .308 and only partly resize the cases. I run them into the die a little more than 2/3 of the length of the neck. At least in my rifle this works great. Chambering and extraction is always reliable and easy.
-
Banned
That's intersting Amat. Like I said, we tested the rifle body steel from Indian 7.62 AND .303" SMLE's and contrary to popular belief, they were all the same...., within the realities/peramaters of steel mixing of course.
Is the EN steel a Chrome Nickel Steel?
Skennerton
's book , if that where the scanned page I saw earlier came from, stated that the Lithgow rifles that failed the tests when converted to 7.62 were (near as I remember) "degraded by use of Carbon Steel rather than Chrome-Nickel Steel".
Australia
has large deposits of Nickel, so a Nickel Steel alloy would be logical for the Lithgow receivers. Nickel Steels are more elastic, and these alloys were invented by an Englishman.
If you have the specs for this alloy it would be useful.
I've found the specs for the US M1917 rifles, which I figured were the same as that used for the P-17. Its a high nickel content steel.
1917
Enfield Rifles
Receiver and Bolt:
Made of nickel steel specificed in US Army Pamphlet no. 3098.
This steel could be made by the acid process, or the basic process, both were accepted.
Acid Process:
Carbon .30% to .40%
Manganese .50% to .70%
Nickel 3.00% to 3.75%
Phosphorus under .05%
Sulphur under .035%
Basic Process:
Carbon .35% to .45%
Manganese .50% to .70%
Nickel 3.25% to 3.75%
Silicon .10% to .20%
Phoshorus under .05%
Barrel Steel specified in US Army Pamphlet no.3098:
Carbon .45% to .55%
Manganese 1.10% to 1.35%
Silicon .20% to .30%
Phosphorus under .06%
Sulphur under .06%
Last edited by Alfred; 06-29-2009 at 12:14 AM.
-
Banned

Originally Posted by
villiers
Me .... I think I´ll keep my 7.62 chamber (very) dry in future. When I recently got the rifle, rounds would not fall into the chamber of their own weight and were sticky extracting. Sent the action to
Germany
´s leading gunsmith (head of the German guild of gunsmiths and maker of gunsmith tools, mainly reamers). He inspected the chamber and tested head space. Told me that headspace was not up to German commercial standards, but well within limits.The chamber was re-reamed in the shoulder area and is now spot on and I now only have to neck size. I didn´t like the alternative advice given by my re-loading expert who advised the use of a special (smaller) die, made for full auto and machine guns. So, is there a difference in size between 7.62 full auto cases and commercial?
I ran down the personal account of the Sniper whose L42 jammed so badly in combat in the Falklands campaign that he discarded it and used a captured Argentine
FAL in its place.
He said that the weather was very wet and the bolt became so still he could barely operate it. He blamed the problem on not having had any oil to put on it, but I've never seen an Enfield that wouldn't cycle without lubrication.
Its likely German standards vary from British
and US standards in a number of respects.
You mentioned this rifle had a scrubbed bolt I believe. Can you be sure the bolt is original to the conversion?
I would not use 7.62 Long Range Special Ball in this conversion, its chamber pressure exceeds the British MOD pressure limits for 7.62 rifle ammunition. That loading was not available while the L42 was in service and its unlikely to be suitable for use in rifles converted to specs in force during the 1970's and earlier. Its a Special purpose cartridge, not suited for many rifles.
There is no EpVat number for the Long Range Special ball and it exceeds the chamber pressure of all other US 7.62 Ammunition that does have an EpVat code number by at least ten percent.
Personally I'd consider the possible cracking or warping of a receiver due to firing a rain wetted cartridge to be a major flaw in a combat rifle.
I guess those canvas action covers paid for themselves many times over.
In 1950 the material for rifle bodies (they made No.1 Mark 3* rifles; my addition) was altered from an EN steel to SWES 48 steel (not heat treated) except for the recoil shoulder and cam recess in the receiver. With this change the rifle receivers distorted when oiled proof cartridges were fired. This was discovered when hard and sometimes impossible bolt retraction was experienced. Large quantities of rifles were rejected. To avoid rejections the authorities ordered discontinuance of the oiled proof. Therefore from 1950 to the end of SMLE rifle production (June 1965) rifles made at Ishapore were proof tested with one dry proof only, although the specification called for both dry and oiled proof.
A bolt action rifle similar to the SMLE Mk. III*, modified to fire the 7.62 NATO cartridge was produced at Ishapore, first in February 1965. Their receivers were made of SWES 48 steel, un-heat-treated, and with the NATO proof cartridge receivers were found to distort with the oiled or the dry proof round! The material was changed to an EN steel so now the rifles stand up better to dry and oiled proof.
There's a lot you can read into what the author has said but I am not going to make any assumptions.
I figure this solves the minor mystery of why some 2A rifles develop excessive headspace after only a few rounds of commercial .308 while others seem to have no problems.
US 7.62 Ball is loaded to 48,000 CUP which is within limitations of the action, but some commercial .308 is loaded to much higher pressures.
Last edited by Alfred; 06-29-2009 at 12:52 AM.
-
Banned
Alfred you are again in error on the pressure rating of 7.62 NATO ammunition, standard ball M-80 is rated at 50,000 CUP or 60,000 PSI (transducer method) average mean temperature
The .308 Win is rated at 52,000 CUP or 62,000 PSI (transducer method)
There is only 2000 psi difference between the .308 and 7.62
The 48,000 cup pressure you are using is for quality control checks in MIL-P-3984J done at 125degrees, minus 65 degrees and 70 degrees. The pressures listed for these tests are as follows”
48,000 CUP at minus 65 degrees
53,000 CUP at 70 degrees
55,000 CUP at 125 degrees
standard ball M-80 is rated at 50,000 CUP or 60,000 PSI (transducer method) average mean temperature 
The .308 Win and 7.62 NATO are for all practical purposes one in the same cartridge
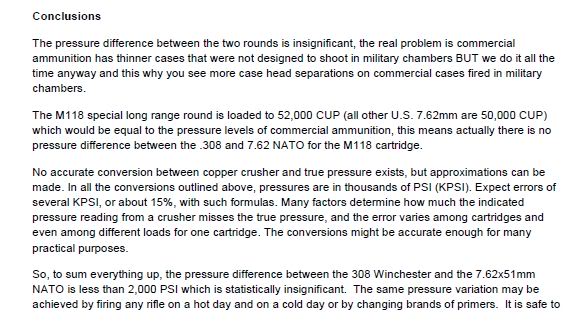