-
Banned
A widened slot in the selector switch allows the trip lever to be moved, this is exactly what you don't want.
You already have a semi auto reciever which can not be converted without considerable modification. The weak spot is the trip lever it's self, if this can not easily be accessed then it can not be easily modifed. Make sure that the housing cover can not be easily removed and you have met the criteria.
I had a good face to face chat with George Fraser about registering an open bolt sten, it was quite an eye opener.
When doing this kind of thing it is easy to get bogged down with minor details and lose sight of the obvious.
Last edited by Mick; 11-11-2008 at 02:00 PM.
-
11-11-2008 01:57 PM
# ADS
Friends and Sponsors
-
Advisory Panel
George Fraser. Office: (613) 993-0038 (1068).
Might as well ask for the FRT number for a homemade open bolt semi auto Mk. II Sten at the same time.
Last edited by tiriaq; 11-11-2008 at 04:08 PM.
-
-
Once I have the innards cleaned up, I will probably tack weld the trigger pin in place so that the trip lever cannot be readily removed. That should help. I have now also welded in a guide block to further limit trip lever movement. Pics to follow later. Sadly, I accidentally fried my trigger spring when it got hit with a welding electrode... on the hunt for a replacement. This has stalled the current build - sadly.
Союз нерушимый республик свободных Сплотила навеки Великая Русь. Да здравствует созданный волей народов Единый, могучий Советский Союз!
-
-
Time for a little Sten history. Some Sten guns suffered from "droopy mag" which was really a symptom of either a worn out mag well plunger or, more frequently, a barrel nut hole that had become oblong over time. This often meant the scrapping of the gun, or sometimes a puncher mag box or newer, larger plunger pin.
Since we are not military with many spares, it may pay to fix a droopy mag. Also, this repair can be used to correct by a few degrees if, like me, you accidentally weld in the collar a few degrees off on one of your builds... oops! But we can fix it, we have the technology...
First we drill out the hole to something larger, in this case 7/16", and tap it. Then we screw in an appropriately sized NON_ZINC_PLATED steel bolt or screw, well coated in permanent lock-tite. Do not tap all the way through, leave the bottom threads tight to get a good interference fit in the hole. Do not go through into the hole for the barrel, stop flush to the hole so the barrel still fits!
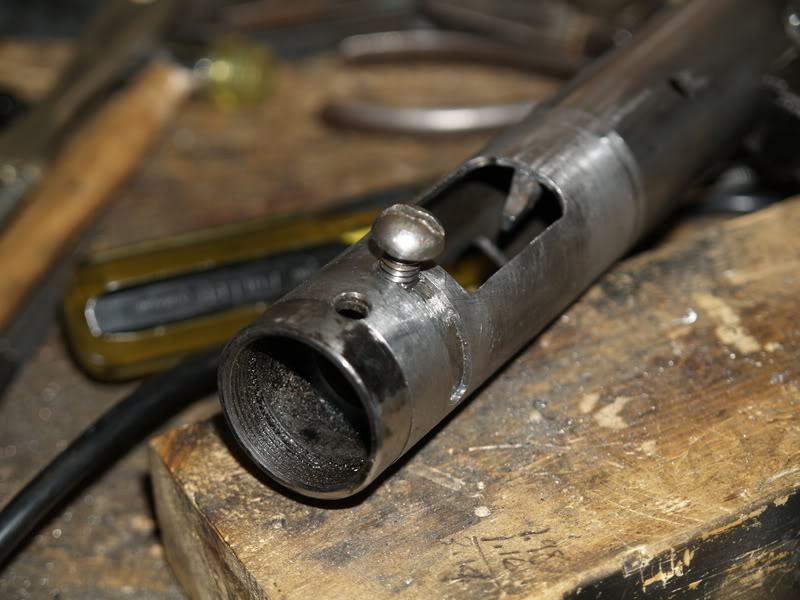
Hack saw off the head and dress it down slightly below flush with a file:
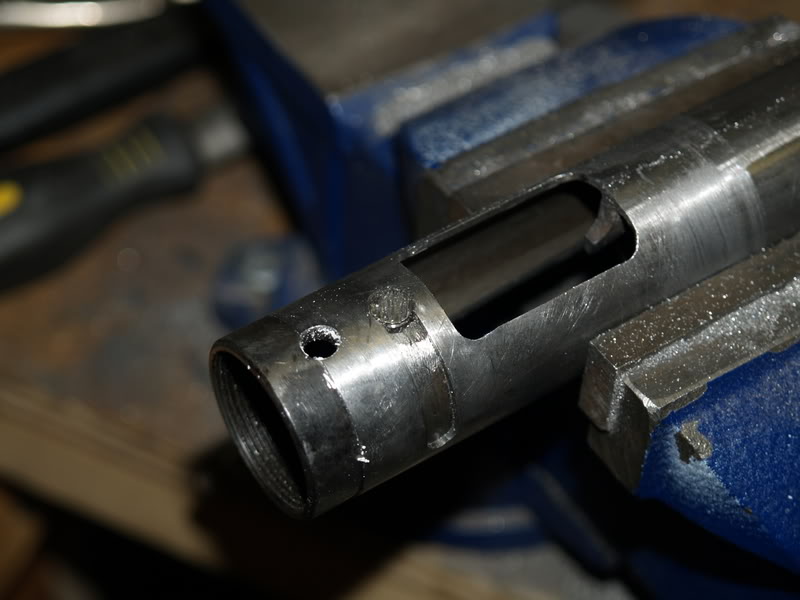
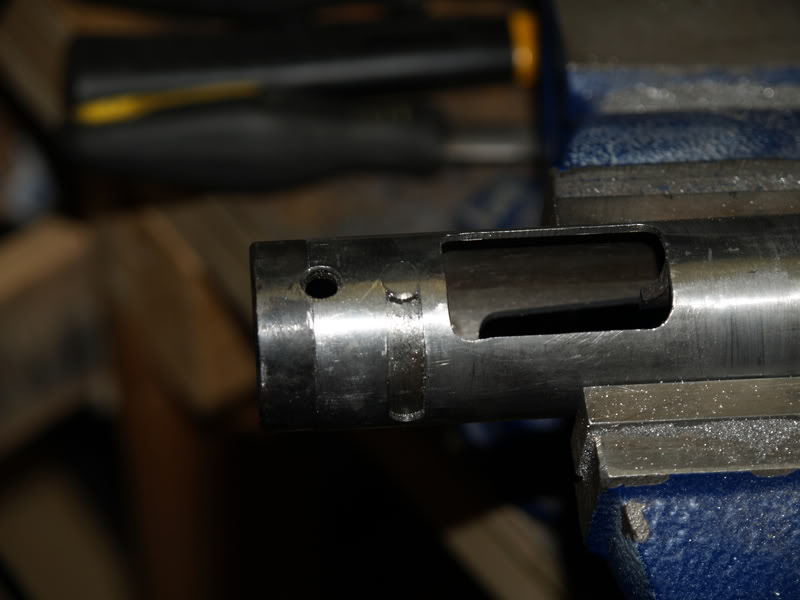
Now crank up the amps on your MIG welder and giver her a good deep plug welding:
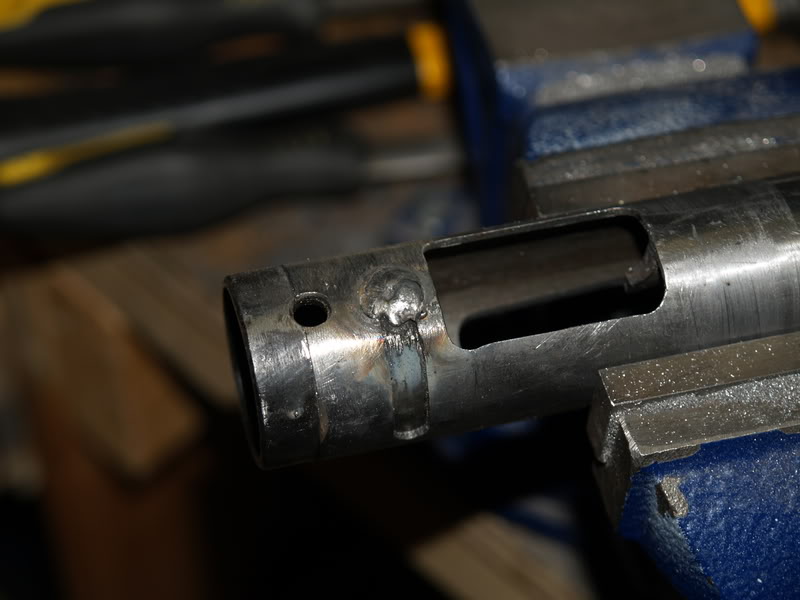
File to match the tube contour:
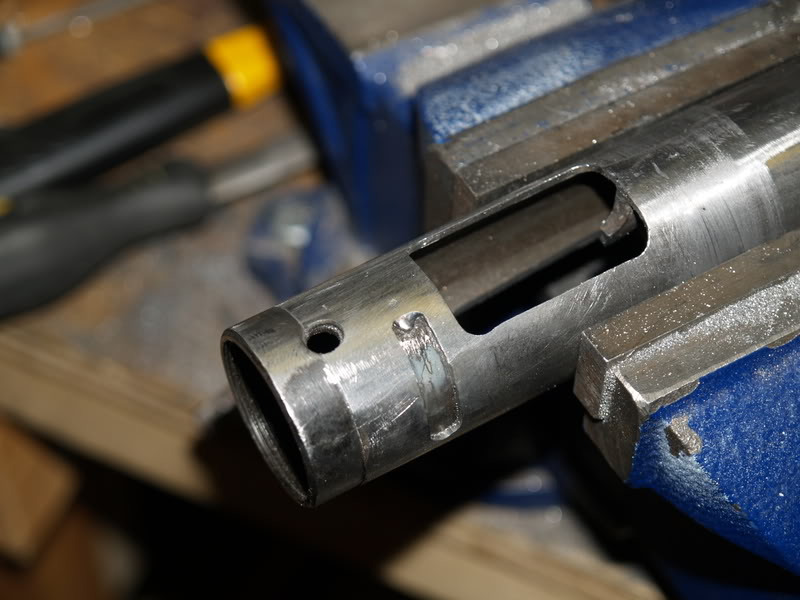
Re-drill the hole and clean up the channel with the mill. DRILL ACCURATELY AND CAREFULLY. Start with an undersized drill bit and finish drill with the proper size drill. You may have to spot-aneal the weld if it is too hard.
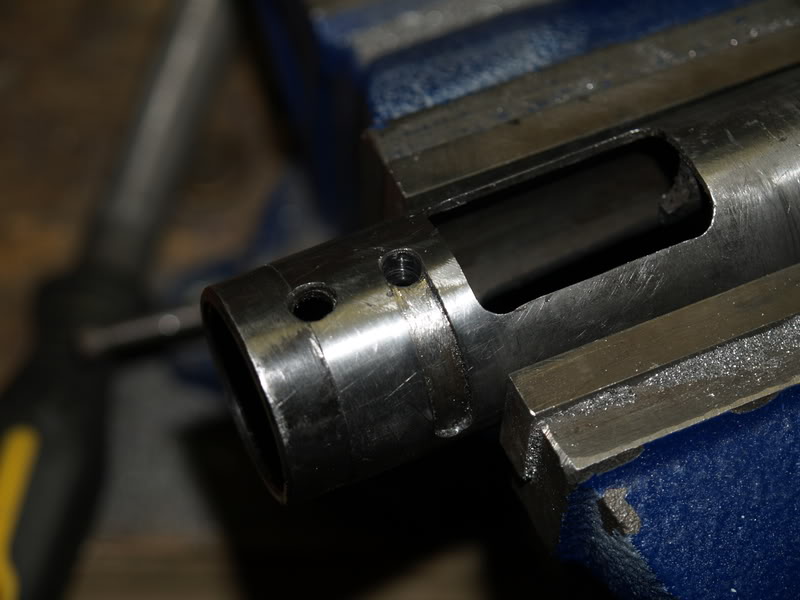
Good luck!
Союз нерушимый республик свободных Сплотила навеки Великая Русь. Да здравствует созданный волей народов Единый, могучий Советский Союз!
-
-
-
-
here are some preliminary design decisions in my quest to devise an acceptable open bolt design. BE AWARE. These design changes ARE NOT YET REVIEWED BY THE RCMP AND MAY NOT GET APPROVED. You would build and submit a gun like this at your own risk as it may get confiscated.
Here we see a steel block that has been cut to fit between the trigger box wall and the disconnector slot. Coupled with the above-detailed modified selector, the trip lever can now not be readily made to move over to the full-auto position and the steel block welded in from behind makes filing out the disconnector slot nearly impossible:
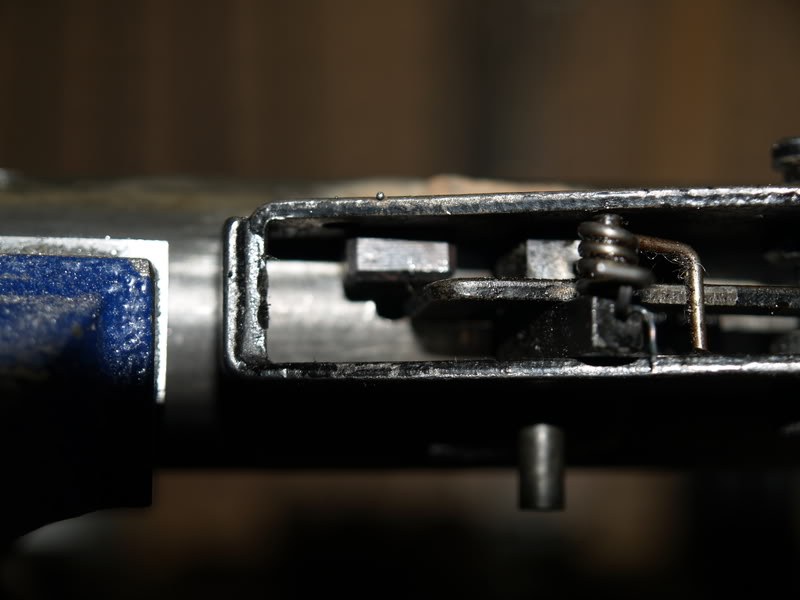
And here is the back side showing the plug weld:
Союз нерушимый республик свободных Сплотила навеки Великая Русь. Да здравствует созданный волей народов Единый, могучий Советский Союз!
-
-
Banned
Is that tig welding ? whatever it is it looks neat.
I have found that by far the fastest way to make the mag well is to use box tubing, it makes a tidy job with minimal effort.
-
Advisory Panel
"Now crank up the amps on your MIG welder and give her a good deep plug welding"....
Cost being no object TIG might well be the preferred system.
MIG equipment is somewhat less expensive. I don't think Claven is using a Linclon Electric welder, but Cdn. Tire has the Linclon MIGPak 140 and 180 on sale quite often. 140 amps and 180 amps maximum output (far more than needed for this sort of work). These units are ready to go for flux cored wire feed, just add a tank of gas for MIG. The larger 180 sells in the sale flyer for $599.95, the 140 for somewhat less. That is about half a TIG.
-
-

Originally Posted by
tiriaq
"Now crank up the amps on your MIG welder and give her a good deep plug welding"....
Cost being no object TIG might well be the preferred system.
MIG equipment is somewhat less expensive. I don't think Claven is using a Linclon Electric welder
Actually, for this latest build, I'm using a 120v Lincoln Electric SP135. I think they discontinued that model last year, but some places still have it in stock. Mine is set up for both flux cored and gas, though in the pics where the weld is spattered in brown residue, I am using flux-cored wire because gas is expensive and I have lots of flux-cored wire lying about, so I only use gas when there is a real benefit to doing so 
TIG is the way to go if you can justify the expense and take the time to learn how to properly use it. For home shops, it doesn't often make much sense though...
Союз нерушимый республик свободных Сплотила навеки Великая Русь. Да здравствует созданный волей народов Единый, могучий Советский Союз!
-
-
Banned

Originally Posted by
Claven2
Actually, for this latest build, I'm using a 120v Lincoln Electric SP135. I think they discontinued that model last year, but some places still have it in stock. Mine is set up for both flux cored and gas, though in the pics where the weld is spattered in brown residue, I am using flux-cored wire because gas is expensive and I have lots of flux-cored wire lying about, so I only use gas when there is a real benefit to doing so
TIG is the way to go if you can justify the expense and take the time to learn how to properly use it. For home shops, it doesn't often make much sense though...
If you can weld like that with a mig then there is little point in getting a tig.
I have a mig with gas and can come nowhere close to the welding you have done on your magwell.
PS another thing I'm useless at is stamping the serial number etc neatly, how the hell do you do it ?
In future I'm not going to weld any visible welds on firearms with anything but a tig welder, a friend of mine welded the magwell below for me with a tig.
Last edited by Mick; 11-14-2008 at 09:57 PM.