-
.....or bedding compound maybe. Would an ill-fitting fore end necessitate a Base Workshops visit?
-
-
10-08-2012 09:07 AM
# ADS
Friends and Sponsors
-
No, fitting a fore-end was a job for a first-class Armourer. But by the time the L42's were at the end of the line, there weren't many Armourers who could fit a file handle - let alone a fore-end
-
The Following 2 Members Say Thank You to Peter Laidler For This Useful Post:
-
Legacy Member
Might I ask why the Armourers would not be able to fit a forend? Is it because the new weapons had little wood so the old wood working skills were no longer taught? If so was the revised training program lacking in any way or did it just focus on skills more pertained to the modern weapons that lack wood?
I just read a very detailed description of an Ordnance overhaul facility in Egypt during October 1942~March 1943 by Roy Dunlop in his book "Ordnance Went Up Front". He includes a very detailed of the work done in the British
overhaul facility. He wrote very admiringly of the British Armourer-Warrant officers and their skills, discusses the apprentice ship program and the high degree of competence of the technical staff.
-
-
Legacy Member
They don't teach those sort of skills anymore. They will be just parts-changers (if that). Deep-level maintenance would be pushed back onto the contractor/manufacturer (though if he's gone out of business because you haven't given him any orders in a dog's age then you're donald ducked).
-
-
Contributing Member
Its not just the army - you try and find a 'skilled' toolmaker that has been apprenticed in the last 15 years.
And I mean one that can use the bench, mill, lathe - grind turning tools from scratch - sharpen drills etc etc.......
-
-

Originally Posted by
waco16
Its not just the army - you try and find a 'skilled' toolmaker that has been apprenticed in the last 15 years.
And I mean one that can use the bench, mill, lathe - grind turning tools from scratch - sharpen drills etc etc.......
It was the curse of the "Modern Apprenticeship" what ended what most on here would call a proper Apprenticeship, even the basics are no longer involved, when I did mine all aspects of the trade apart from welding were taught, bench fitting, lathes, millers, shapers, horizontal grinders, electrical work, sheet metal work, brazing, pneumatic and hydraulics, all that was in a training school in the first year, must admit I,m still s**t at sharpening drills though.
Whats left of what I made at 16 (all hand made to within a tolerance), only thing what we got was the screws which were produced by whoever was on the capstan, even the wing nut was hand made and the handles were square blocks to start with, even the name plate was produced with a starting hole and then cut using a abrafile,
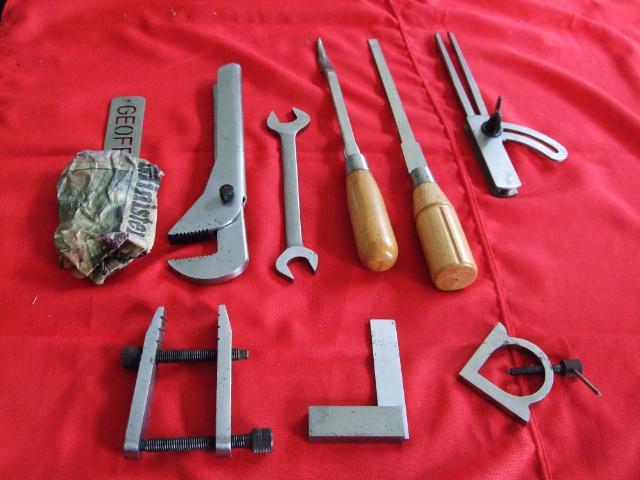
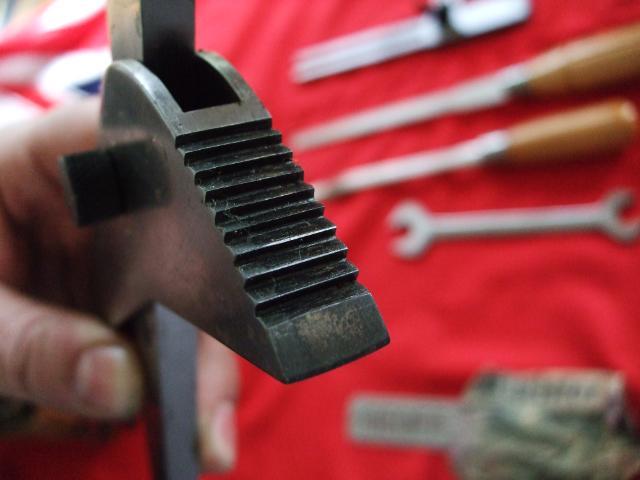
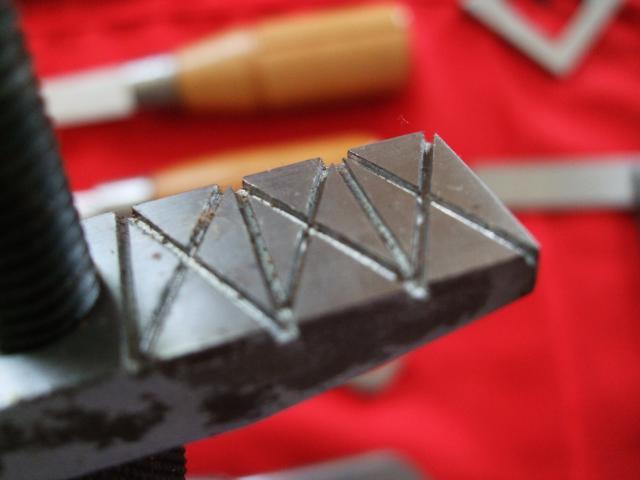
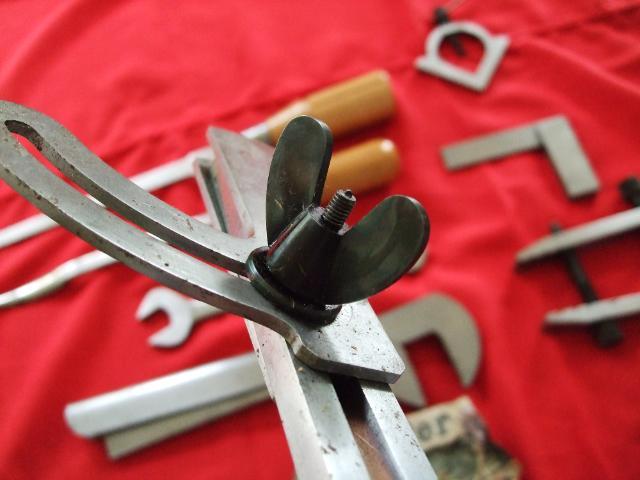
-
The Following 6 Members Say Thank You to bigduke6 For This Useful Post:
-
MAGNIFICENT selection of apprentice made hand tools............... It just shows the versatility of the old apprentices. When I needed a new crosshead lead screw and nut for my little Myford lathe, I just got a bar of steel and length of bronze and turned a matching set! Probably cost more that a new one but................. I canm sharpen all the drill sizes and would regularly pick a few blunt ones out of the bin then sharpen for my own use
Thanks for showing us those Big Boy! We did the welding bit during my apprentceship but to be honest, I might go to college and see if I can't master a mig or tig now
-
-
Legacy Member
Big Duke
Nice set of tools.
Better than a bought one!
The only downside with making something yourself, is that you always know the area that is not quite perfect even if no one else ever notices.
-
-
Thanks Peter, Paul, If we even touched a welding rod there would be uproar in the boiler makers union, brazing was our limits even the coppersmiths were not happy, then again they never were.
Paul, We never had much option as these were made to engineer drawings, if it wasnt up to scratch it went in the bin, all the tools above gained me 98 -100%, everything before we started had to be square and scraped flat on all sides, tolerance on this was tight and after only getting it passed, you could then begin to mark out, the one that caused most injuries was the grab (not shown) a very robust small clamp, (think of a g camp but 1" thick) to cut the centre out we had to hacksaw so many sections and then hand the hacksaw in, then it was a case of removing the metal with hammer and chisel !!, the F word was mentioned many a time.... of course all that training goes out the window once we were let loose in the shipyard, there you do it the fastest and easiest way possible,
Last edited by bigduke6; 10-10-2012 at 10:48 AM.
-
-
My bench fitting apprentice master was Mr Surtees. His maxim was that '......near enough isn't good enough. But exactly right is near enough'
-
Thank You to Peter Laidler For This Useful Post: