-
Got the block off and discovered that the rear does seem to have plenty of unused (untapped even!) bore that ought to help line things up. I'm hoping that it will loosen, but that never seems to work out w/ aircraft parts!
Dab nag stinkin' screw portion that came out is really pretty hard- much more than it ought to be. I'll try and check it on a Rockwell hardness tester in a few days when I see the fellow that has one.
Thanks for the offer of a new block, but if this operation doesn't work there's another that I pulled from an incomplete Long Branch that has a 1955 Faz. bbl. assembly.
Do the block retaining pin holes line up from rifle to rifle, generally? They sure DON'T on M-16s!
BTW I think this is the first part I've broken on a L-E variant! Must not be trying hard enough...
.
-
-
12-05-2009 08:23 AM
# ADS
Friends and Sponsors
-
-
-
Banned
-
Your pictures brighten me up on a dreary Sunday Morning Ed. Who could have thought of the Polish hand drill like that!
-
-
Banned
Your pictures brighten me up on a dreary Sunday Morning Ed. Who could have thought of the Polish hand drill like that!
A retired Colonial Rebel with too much time on his hands who has a Polish mother-in-law.
Aim High, U.S. Air Force
-

Originally Posted by
Edward Horton
Remember when you get the sight all back together and tighten the new clamping screw, to tighten the screw until the threads start to smoke and then give it two full turns more.
I’ll let you borrow my surplus NASCAR impact wrench.
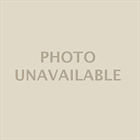
I think that's how it was installed the last time!
FYI The screw head itself measured ~8Rc, not hard at all. However it quickly increased in hardness as we moved down the sectioned threads, going from 22Rc (OK) hardness upwards! Judging from the difficulty drilling from the tip towards the fractured portion, it was probably 50-60Rc at the tip. Bad day at the heat treat facility, I guess.
BTW If that lug bolt pic isn't photoshopped, it's amazing! Misspent too much time at the GT "trade school" playing at failure analysis...
-
-
Banned
Jmoore
The next time your in a garage or service station ask yourself when was the last time the impact wrenches were checked for torque calibration. On aircraft they were never used because they were unreliable, torque wrenches were always used and they were checked and calibrated every 90 days.
Below impact wrench over torque. 
-
Nice ductile failures. I think that one difference w/ these abused fasteners and the ones we failed is that the ones you show are too "short" for whatever they were they were installed. A/C fasteners, as you know well, are selected so that the unthreaded shank is run as close as possible to the nut+washer resulting in generally short thread lengths and -failures- at or near the thread origin if overstressed.
Not only do I not use impact wrenches except when disassembling fasteners that won't be reused (in any application, including farm equipment) but my torque wrenches for critical work are also calibrated. Not to mention my other measuring equipment....And firearms people think the govn't have too much involvement in their lives!
-
-
We don't use impact wrenches (or whizzy-wig hammers as we call them) either and our torque wrenches are calibrated annually, together with our gauges and other measuring equipment.
Nuts, screws and bolts are a science in themselves....
How I cringe when I see the tyre (or tire as you wild untamed colonials call them...) garages where they whizzy-wig the wheel nuts back onto the wheels/hubs. No wonder you never get them off again at the roadside
Good technical thread here guys..........
-
Thank You to Peter Laidler For This Useful Post:
-
FREE MEMBER
NO Posting or PM's Allowed
How I cringe when I see the tyre (or tire as you
wild untamed colonials call them...) garages where they whizzy-wig the wheel nuts back onto the wheels/hubs. No wonder you never get them off again at the roadside
Hey I resemble that remark.