-
Advisory Panel

Originally Posted by
tankhunter
a Nut & Bolt was fitted transversely across the Bolt in the recess.
That's right. I remember that pic now. I have that book...
-
-
06-21-2016 08:09 AM
# ADS
Friends and Sponsors
-
Legacy Member
Vincent, does the cover which you have, that is welded, have a manufacture's mark on it and if so what is it, please? I have just taken a cover off one of my U.K. made Stens with the dimple type attachment and with the manufacturer's mark of S106 and there is certainly no welding at all on this cover. From memory I think that all my U.K. Stens have the same manufacturer of cover but the Canadian
Sten is likely to be different and I haven't had that cover off yet to see if there are any welds. The thing with form tooling is that it is not an exact science as you are trying to stretch and squash the metal all at the same time, in several different directions, and one of the potential problems is that the metal will sometimes crack/split as it is being formed. From personal experience I have normally found that this problem can usually be overcome by an increase in radius of where the metal is being formed in the tool. If your cover has a different maker to the example which I have been examining I would suggest that the manufacturer had problems with cracking of the cover while being formed and the simplest solution was to introduce 2 slits/cutouts into the blank followed by welding after forming. It is surprising that if one manufacturer found it necessary to introduce several additional operations which were not required by alternative suppliers.
Looking at the cover in detail I have to say that whoever the Toolmaker was for J. W. Spear & Son Ltd (S106) he/she made an excellent job of the tool. The tool has produced a very smoothly formed cover with very few ripples and bend marks etc which are sometimes seen on formed parts.
-
-
-
FREE MEMBER
NO Posting or PM's Allowed
wasn't the trigger cover stamped out in one piece and then formed in a butterfly press and the curved section brazed together onto the central section ??
-
Yep, that's right. Thousands were done this way PhilB. And this was an unfoolded plate example shown in the book The question raised by F10 (thread 42, para 1, last sentence) is that more than likely, that contractor was making the same piece but using the simple fly-press in a small garage in Maidenhead as opposed to a large hydraulic press in a well equipped fabrication shop in Bloxwich.
Different manufacturers used different methods. Just so long as a) they were sanctioned to do so and b) the product functioned as it was intended
-
Thank You to Peter Laidler For This Useful Post:
-
Legacy Member
It would have been a power press with a large flywheel on the side of the press as apposed to a hydraulic press which doesn't have a flywheel, I suspect. This would have been in the days before guards were required by law to be used on power presses in the U.K. and accidents were relatively common such as the loss of finger/s or even a hand.
-
-
Ok....... Hydraulic press, power press..... The point I was making was that different contractors were using whatever machinery they had. But no doubt, with 4.2 million covers being produced somewhere, someone will have been using each sort. They certainly were because I spoke to someone who personally punched out the return spring caps and cups
-
-
FREE MEMBER
NO Posting or PM's Allowed
another on the sten bolt....was the firing pin machined on the bolt face or a hole drilled and an insert put in ???
-
Same again. Different manufacturers, different methods. Those made at Sterling were machined from solid. Some bronze ones a steel stud was an interference fit
-
Thank You to Peter Laidler For This Useful Post:
-
Legacy Member
Peter, what I would be interested in is if some-one could produce a cover stamped with S106 as I referred to above (post 42) but made in the way you describe which I call the knife and fork method. You sometimes see the "knife and fork" method used early on in the production of a metal part before proper "hard tooling" has been made. It is quite possible that there are covers made the way you describe with the S106 mark but just haven't surfaced yet. The other advantage which you have also stated is that it doesn't require a large press but the disadvantage is that the "knife and fork" method is more labor/time intensive. I will try to get round to having a look at my Canadian
Sten and seeing how the cover on that was produced.
-
-
Legacy Member

Originally Posted by
Flying10uk
Vincent, does the cover which you have, that is welded, have a manufacture's mark on it and if so what is it, please?
There are no manufacturer’s markings on the cover. There is what looks like an index mark on the left side, but I don’t know why it’s there. Maybe it was used in manufacturing?
The only markings I have found so far are on the magazine housing, “TMT IV”, “40147” and the Israeli IDF property mark.
I understand your interest as a toolmaker in how these covers were made. I don’t know much about stamping parts, so it’s interesting for me learn from someone who does. I do know a little about welding and whoever welded this Haganah cover was very good. Remember, this was done before TIG welding was widely available. The steel is only 0.036” thick.
Here are some pictures of the Haganah cover and a MK3 Sten cover made by Lines Bros Ltd.
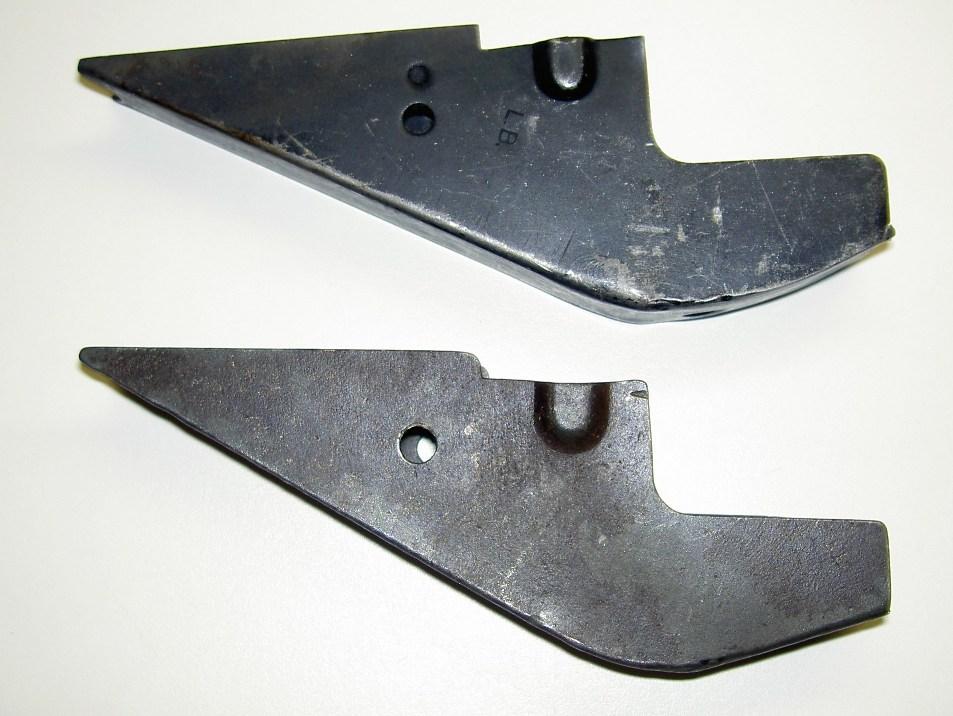
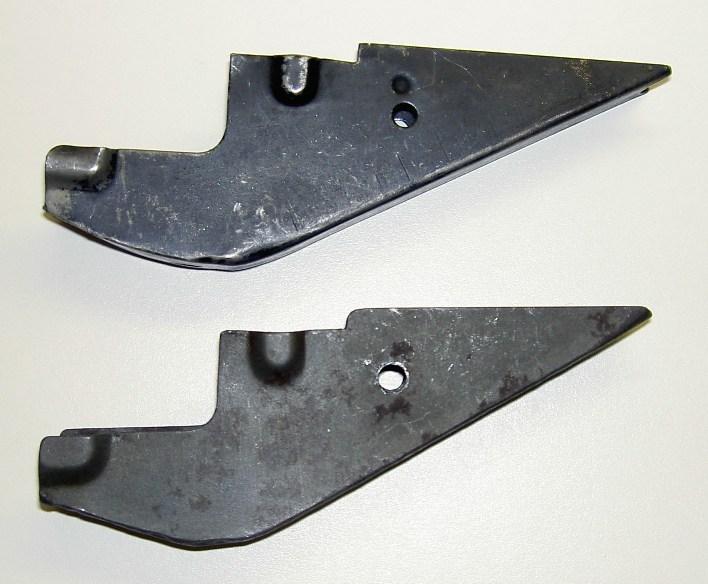
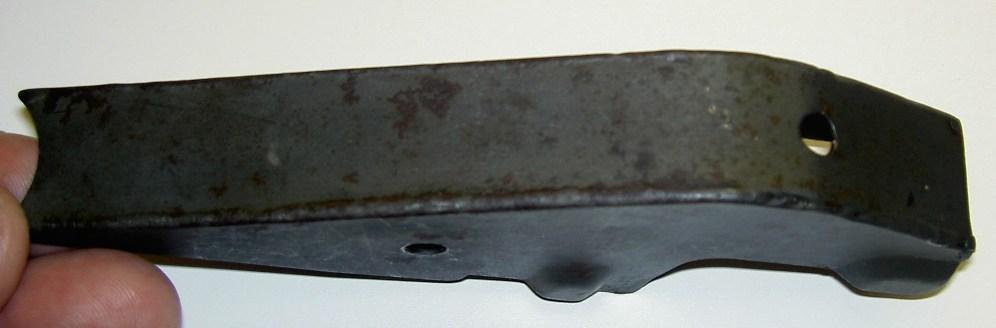
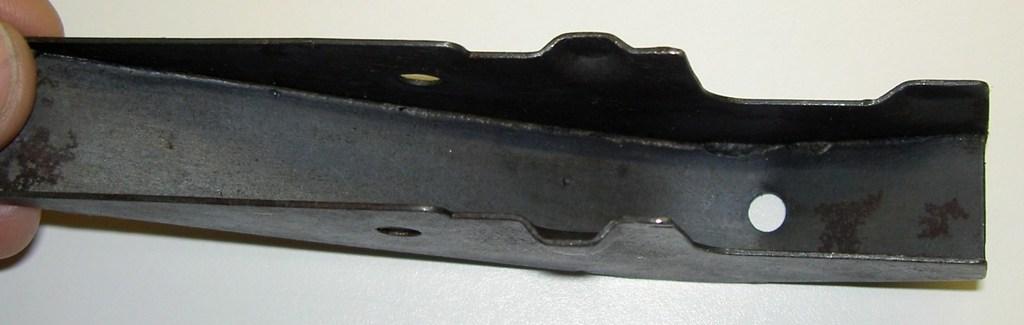
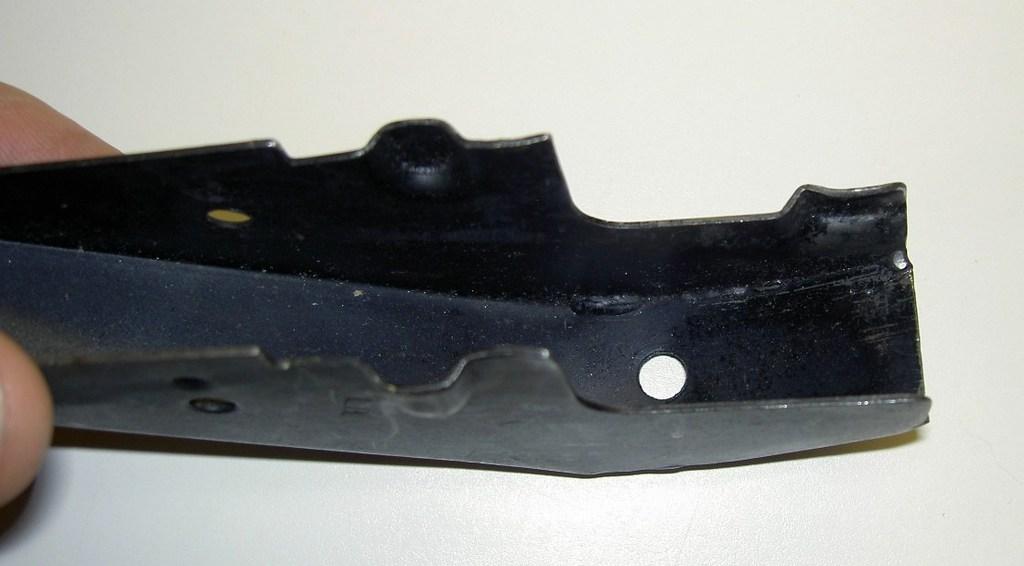
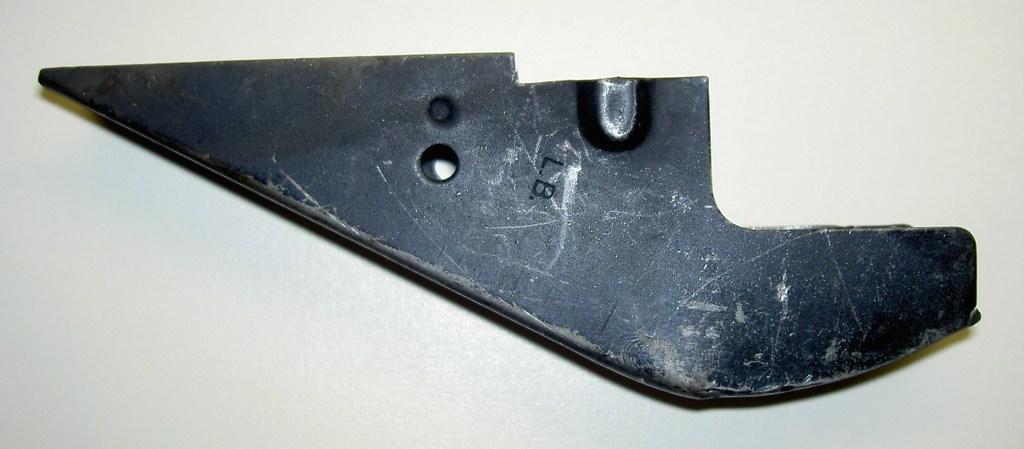
As you can see, the Lines Bros cover was made with rear welded. That’s interesting to me because they were very good at stamping.
The Canadians seemed to be quite advanced at stamping parts back then. Their version of the Mk4 Sterling, the C1 SMG, also used a lot of stamped parts. I have been able to duplicate most of the parts I was missing using my small 50 ton hydraulic shop press. The bayonet attachment is beyond my ability to press, so I am making it from two parts and welding them together. Then I will machine it to look like it was stamped.
Last edited by Vincent; 06-23-2016 at 11:37 AM.
-