-
Legacy Member
-
-
06-23-2016 11:40 AM
# ADS
Friends and Sponsors
-
Legacy Member
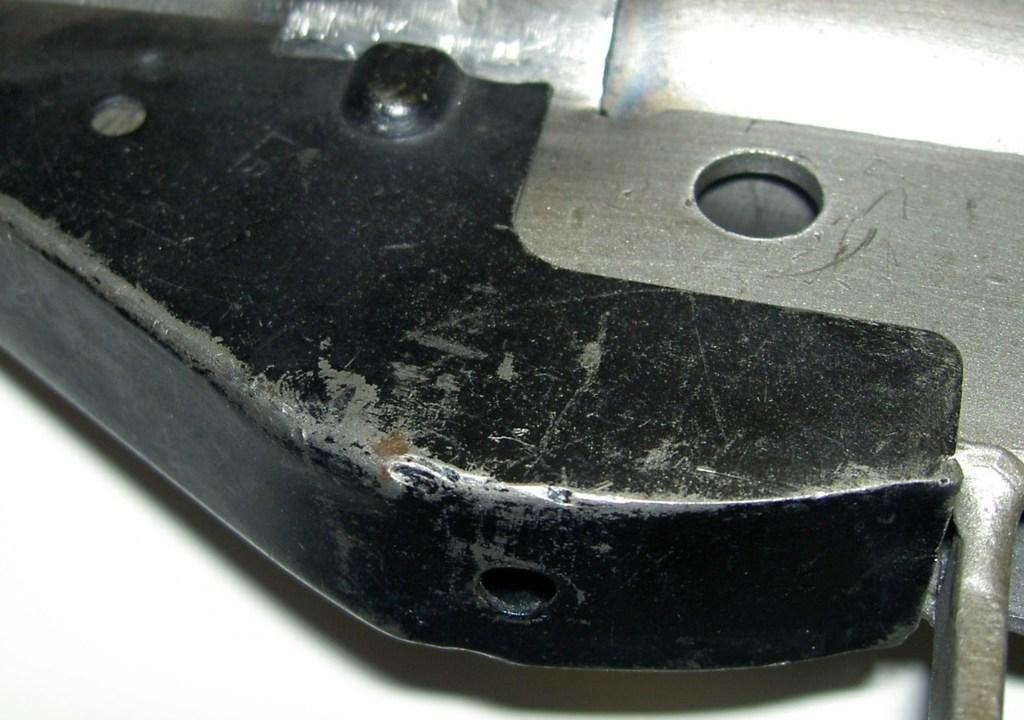
The LB marked cover.
Compare it with the S68 marked cover, and you can see there is variation at the same manufacturer.
-
-
-
Legacy Member
Thanks for the pictures vincent. Although I don't have any spare covers I do have around 5 Stens, at the last count, and so can examine the covers from those guns. I take it that your last post is a 4th cover by Lines Brothers and not the Canadian
cover (Long Branch)? I've got a feeling that the cover on my Canadian Sten has been made differently to your example but can't be sure until I get it out and have a detailed look.
-
-
Legacy Member
-
-
Legacy Member
Sorry vincent, I completely missed post 50. So looking at the picture of the Lines Brothers cover in post 50 I would say that the tooling to produce this cover would be a relatively simple affair. The top tool or punch, to some, would have it's lower edge/surface which hit the blank (cover) either completely flat or flat with a small rad at one end. The bottom tool or die would have been 2 parallel blocks of metal secured to a base with screws and dowels. The distance between the 2 parallel blocks would have been the width of the cover. Almost certainly there would have been a spring loaded pressure pad between the blocks to eject the cover from the tool after forming. The die blocks probably also incorporated perhaps 6 location pins for the blank. This type of tool could easily be operated in a Fly Press (hand press). Its when you try to start forming the radius that you would need a power press.
With regards gas welding, years ago welders were much more skilled in the use of Oxyacetylene (gas) welding than they are today. There was none of this fancy Tig and Mig equipment.
-
-
Legacy Member
Thanks for describing the tooling. It sounds very similar to what I use for pressing AK47 receivers.
What causes the galling you see on the Lines Brothers cover?
-
-
Legacy Member
I take it that by "galling" you mean deep scratches/grooves? On the edges of the die blocks it is normal practice in toolmaking to radius these corners off so that as the metal is pushed down into the die it flows over the edge without digging in too much. With the Lines Brothers cover these rads either require increasing slightly or, through use, the tool edge has "fired up". This is where tiny amounts of the metal being worked has transferred itself to the tooling causing a rough surface to build up on the tool which in turn then scratches/marks the metal being worked. Normally this can be removed and the surface cleaned up by the use of an oil stone and emery cloth but not with power tools. It is normally advantageous to use an oil or thick cutting liquid as a lubricant when working with form tools in order to help the metal slide over the tool without binding.
-
Thank You to Flying10uk For This Useful Post:
-
Legacy Member
Thanks. I would never have guessed it was caused be metal being deposited on the tool.
-
-
Legacy Member
It surprises me that the Lines Brothers cover isn't made the same way as the Spear & Son cover i.e. in a single hit, or perhaps they did? They were obviously reasonably skilled in the art of sheet metalwork to be able to produce the MK3 Sten.
-
-
Legacy Member
That surprises me too. Lines Brothers might have gotten around to stamping them at a single hit at some point. I haven’t seen one of their covers made that way, but there is variation in the ones I have. So it’s quite possible they could have made some that way.
It’s also surprising to me that the Long Branch cover is not made from a single stamping. Though we must consider how new this type of production was for guns at the time. Before the Sten guns were made the traditional way. The Sten was a totally new way to produce guns. Like any new production method there’s always a learning curve.
Parts of the Haganah cover are stamped. That makes me wonder why they didn’t make them like the others, with only the back welded.
Was it your toolmaker background that got you interested in the Sten?
-
Thank You to Vincent For This Useful Post: