-
Legacy Member
Dimples on receiver and bolt
This is a really dumb question, especially since I used to know the answer many years ago, but "Old Timers" has scrubbed it from my brain. What is the meaning of the small dimple on the front of the sight bridge and the bolt head. It seems to me it has to do with rebuilding or servicing, but mine is original and has the marks. Thanks in advance. Inquiring minds want to know.
Information
|
Warning: This is a relatively older thread This discussion is older than 360 days. Some information contained in it may no longer be current. |
|
-
-
09-21-2012 11:37 PM
# ADS
Friends and Sponsors
-
Off the top of my head, it indicates those parts have passed proof testing. I bet the dimple on your new Inland receiver is "on top" of the finish, showing it hasn't been reparked. - Bob
-
-
DECEASED
I have always understood it was a simple "Hardness Test" of the metal, done with a pin punch, but I may be wrong ? ?. Mike.
-
-
Legacy Member
That's it - verification of hardness with a punch. I have no idea how they controlled that process unless they had a machine for it. I mean, how do you hit a punch with a certain diameter, hardness and tip shape with a hammer, to deliver an exact and repeatable force? To do that by hand is impossible, but perhaps it didn't need to be as technical as I'm trying to make it. Maybe you just take a center punch and ball peen hammer and give the object a medium shot, not like you're trying to drive the punch through it. After doing a few hundred bolts, I imagine you would see and feel a difference if you hit a 'soft' one.
-
-
Legacy Member
Thanks, now I feel better. My dimples are "on top" of the finish, so it is not a repark.
-
-
Legacy Member
Proof testing if I remember right.
-
-
Advisory Panel
(Deceased Feb 2023)
Hardness testing on the bolt and receiver is incorrect. The punch marks are applied when the bolt and receiver have passed the High Pressure Test. The barrels were marked with a P.
Each rifle, bolt, barrel, and/or receiver had to be tested with a High Pressure Test Round. It applied to the Garand, Carbine, M14
, 1911A1, etc.
Below shows an M14 NM Manual and the punch marks.
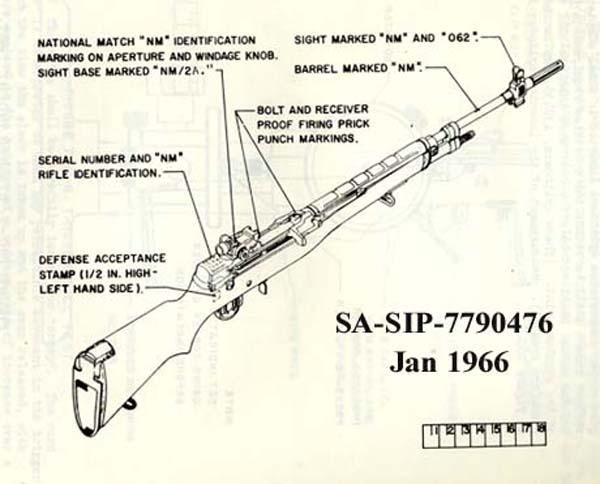
Each proof fire had to be done under safe conditions. Sometimes the actions were fired remotely from another room, depending upon how the contractor set it up. The safety set up had to be approved. On the left is a carbine, on the right is a carbine barrel. Both are show being High Pressure Tested.
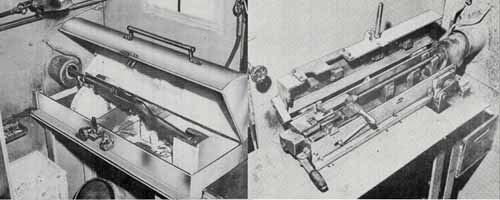
That Hardness Test punch mark has been a myth for years. Not on the Bolt, or Receiver.
-
The Following 7 Members Say Thank You to Bill Ricca For This Useful Post:
-
A Rockwell "C" series hardness test uses a well defined angled punch that is preloaded and then loaded again to a specific force, leaving a very small indentation, the depth of which is measured by the machine using the punch shaft displacement into the metal before it's removed from the machine. (There's some older methods that measure the dimple by other means, but they wouldn't apply here, either.) Regardless, a Rockwell dimple is VERY small and regularly shaped, not at all like whats found on bolts, etc.
The hardness test would also not be accurate except on surfaces that are solid from the indentation site to the bottom of the test piece. You want no holes in the area! Some areas on a bolt lug would be OK as they're solid. But a bolt body has at least the firing pin hole bored through it, so that area is no good.
(BTW, I'd estimate a Rockwell punch mark to be maybe 0.010 0.015" max. in diameter on normal action parts. So small it's useless for an inspection marking.)
Last edited by jmoore; 09-22-2012 at 06:47 PM.
-
The Following 2 Members Say Thank You to jmoore For This Useful Post:
-
Legacy Member
Proof testing it is! That makes sense, as the barrel also has the small P that Bill describes. Thank you Mr. Ricca!
-
-
Advisory Panel
(Deceased Feb 2023)
There are some barrels that have the P and the punch mark inside the P. I guess those were spare barrels that were tested and P marked. Then assembled in a rifle tested and the punch added to the P. Just a guess.
BTW this shows why you can never believe advertisers calling they commercial barrels "Mil Spec". Many do not know what Mil Spec means. No commercial barrel has ever been tested with a GI High Pressure Test Round. That ammunition is almost impossible to produce, unless you have a large GI contract and get the ammuntion from Ordnance.
On the fun side look at the M14
Picture and see the military description of the punch mark. That word cannot be used on many forums "Prick Punch Markings". I could not post it on some forums due to the nasty word.
-
Thank You to Bill Ricca For This Useful Post: