-
Advisory Panel
Interesting, Interesting, Interesting...can't wait to watch this develop. Also I'd like to see how it's all arranged parts wise in the end, if you please...for the engineer in all of us...
-
Thank You to browningautorifle For This Useful Post:
-
04-11-2014 11:05 AM
# ADS
Friends and Sponsors
-
FREE MEMBER
NO Posting or PM's Allowed
Interesting, Interesting, Interesting...can't wait to watch this develop. Also I'd like to see how it's all arranged parts wise in the end, if you please...for the engineer in all of us...
Will do! I am curious as well. I will dry fit all of the trigger and hammer components just to see how the function is. I can't find anyone whose posted photos of that.
I also have to clean up my ejector tab and size the slot so it fits snugly. Also, the extractor pin in my old bolt is stuck. I do not have a drift pin to knock that out. Was hoping not to have to buy another set. We'll see on that issue.
Fitting the AR firing pin into the bolt with the spring; when the hammer is pressed fully into the recess and held, the pin does not protrude. I suspect the inertia of the hammer striking the pin pushes it through the opening in the block face and onto the base of the primer, and then the spring causes the pin to retract back beneath the face of the block.
-
Advisory Panel
I take it that round stock in the pic is the "Hammer" and just the inertia drives it against the firing pic...?
-
-
FREE MEMBER
NO Posting or PM's Allowed
-
The inertia firing pin is a mechanical safety feature (I expect that you are all aware of this - hopefully) that means that unless there is the full force of the hammer blow, it won't protrude with sufficient force to detonate the round. We used to do a classroom test with Browning No2 pistols to test this theory which meant dropping the pistol on the hammer to see if the FP would strike a dummy round sufficient to pop the primer. So presumably this is the safety reason for the single shot Sten to prevent an accidental discharge unless it is from a full force of a hammer blow.
This used to raise all sorts of questions such as hard primer material etc...... This eventually caused several modifications to the hammer spring strength due to different ammunition being brought in. This included several uprated striker springs followed by ever greater hammer strength springs and so on and on. Instead of just going back to basics!
-
-
Advisory Panel
The floating inertial firing pin is a BATF requirement for semi auto Stens made in the US, along with closed bolt operation. If the firing pin isn't a floater, defeating the disconnector function could result in burst fire, as the hammer follows the bolt foreword. If this were not a BATF requirement, a full length firing pin - or even a one piece hammer/firing pin would be an easier way to go. A floating inertial primer is a safety factor, but that is not why it is mandated.
A floating, inertial firing pin will contact the primer when the bolt closes, but should not have enough energy to fire it. An example is the AR-15 type rifle - invariably if a round is ejected, there will be a slight mark on the primer. The US closed bolt semi auto Sten designs use AR-15 firing pins, no doubt because the pins are readily available at low cost.
Some US do-it-yourself designs use a original bolt, altered for closed bolt operation and hammer or striker ignition. This requires extensive alterations, of course.
Last edited by tiriaq; 04-12-2014 at 07:33 AM.
-
Thank You to tiriaq For This Useful Post:
-
FREE MEMBER
NO Posting or PM's Allowed
Thanks the great info on the firing pin. I had not considered it as either a safety feature or a BATF requirement. I sincerely appreciate the comments as I am learning much about my new weapon.
I sized the slot in the receiver tube to the ejector, and recessed it slightly so that there will be a lip which provides room for some welded metal. That should provide a good bond between the the and the ejector. The ejector fits snugly in the slot with sufficient room between the groves on the block. I will still use paper shims between the ejector and the block during welding to prevent it from accidentally being moved.
I also need to clean up the ejector a bit.Too many file marks on my hand made piece.
I'm thinking of using a paper shim and a piece of aluminum foil in the groove between the block and the ejector to prevent weld splatter on the block. Sound okay?
-
FREE MEMBER
NO Posting or PM's Allowed
Need some help here!
Upon dry cycling the breech block into the safety slot on the receiver tube, I noticed the block impacts the ejector and will not go full forward into the safety slot. The images shows the problem.
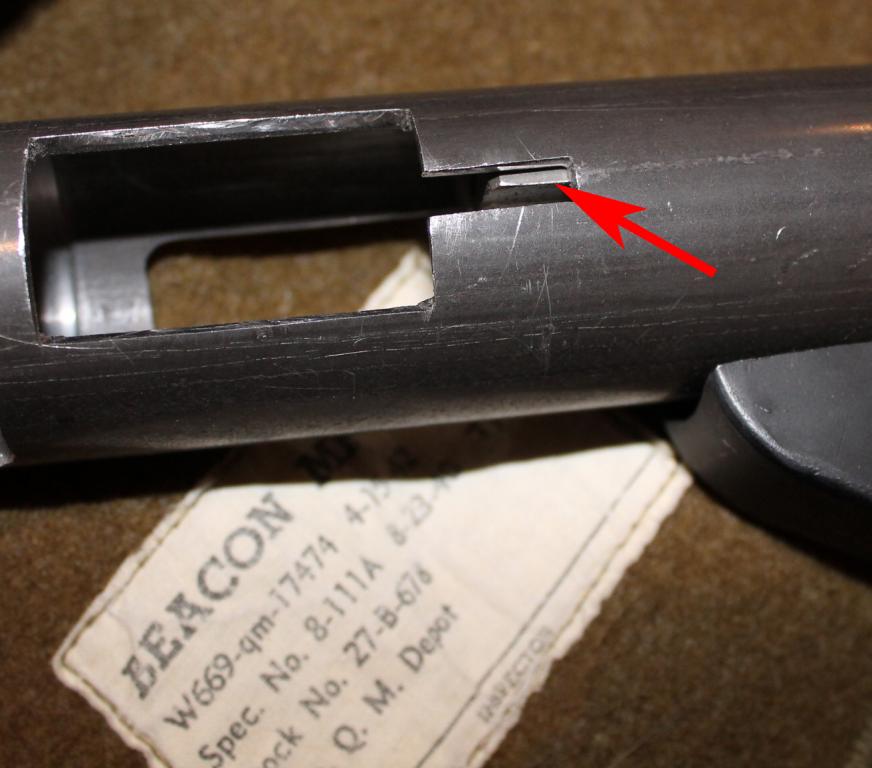
I figure the only reasonable option is to file the ejector to make it skinnier so that the bolt grove will pass over it.
Another option would be to file off a bit of the rear of the ejector so that when the breech moves forward and into the safety position it will not strike the ejector.
I could also not worry about it and the bolt will just not travel fully forward when rotated upward and into the safety slot. I am concerned about this option as repeated slamming of the bolt on the ejector will cause both the bolt and ejector to wear at the point of contact.
If I were to do this again, I would mill the safety slot about 5/16" farther aft on the tube as opposed to where it is depicted on the template. That way when the bolt handle is rotated upward and into the safety slot, it will be that much farther aft and not strike the ejector.
What do you think is the best alternative to rectify this issue.
Here's another image of the issue:
Last edited by 17thairborne; 04-12-2014 at 11:58 AM.
-
Advisory Panel
SAS bolt also fouls the ejector. Even prevents the bolt from going all the way into battery. Easiest to just alter the ejector to clear the bolt.
Found this out on my first project, had to alter the ejector after it was welded in place. Much easier to do before welding.
The safety cut in the main casing is sort of awkward to use - to rotate the bolt handle up and into the slot, the guide rods et al also have to rotate. The whole thing has to be dragged around.
There are ways to alter the selector into a rotating or crossbolt safety.
-
-
FREE MEMBER
NO Posting or PM's Allowed