-
Contributing Member
Tool for rear Handguard rivets?
I'm building a few handguards and am wondering what the proper tool for the small crush rivets that hold the Handguard springs in place is and if there is anything like it available commercially. I have steel rivets and it's proving to be quite the challenge to make them work to say the least.
A mandrel inside the spring may work but finding some HSS round stock and then carbide drill and lathe bits to cut it is a lot of mucking around and costly.
I've tried boring the end of a punch round to hold the rivet head on one side, then did something similar on the other and tried squeezing them in the vise. I also tried smacking them with a hammer, also no good. Any better idea that won't have me ruining handguards at an alarming pace?
Information
|
Warning: This is a relatively older thread This discussion is older than 360 days. Some information contained in it may no longer be current. |
|
Last edited by flying pig; 04-20-2014 at 04:09 PM.
-
-
04-20-2014 04:06 PM
# ADS
Friends and Sponsors
-
I can safely say that we were never supplied bare handguards. They ALWAYS came as a GUARD, HAND assembly, upper. Always as an assembly. We did have loose rivets but they were a general G1 VAOS item, made by a small rivet makers in Aylesbury. I seem to recall that the same brass rivets were used to re-rivet new catches onto the No8 telescope box
Like I always say, while the individual parts were shown in the parts list, you have to remember that the parts list is a list of PARTS and not a list of AVAILABLE parts. I wouldn't mind betting that these brass rivets are available by the bucketful on Ebay under model engineers supplies.
I'm not sure that you'll need anything more than a mild steel anvil and former to rivet brass
-
The Following 4 Members Say Thank You to Peter Laidler For This Useful Post:
-
Contributing Member
I was afraid you would say that Peter!
The brass ones for a Lee-Enfield I don't think would be too large a problem. It's the steel ones for the Ross I'm having troubles with. I've built a stationary mandrel for my vise that will hold the springs fairly snugly in place. I can mark the location of the holes on the springs on it and if I stick some locating dowels out of the mandrel I should even be able to use it to mark the location of the rivet holes in the Handguard. Then in thinking I can slip the rivets in from the outside and using the same holes I've used for the hole marking dowels I should be able to give the rivets a solid whack on the head with a punch I've cupped the tip of in my lathe. After all this work it had better pay off! Probably drastically over-built but if it saves one Handguard it's worth it. The steel rivets aren't particularly hard, just not easy to manage that's all.
Another case where I should have stopped to think first.
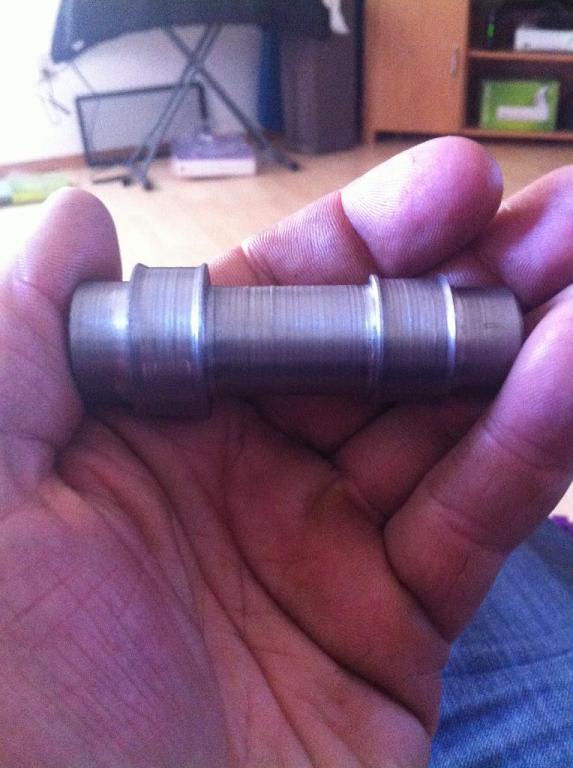
I'll likely weld a piece of flat bar on the bottom so the vise can hold it at a 90* angle to my body and give it a solid point to bite. Time to drill and mark some holes and try it out.
If this does work I will build another for the No1 MkIII rear handguard and for any other application I may run into.
Last edited by flying pig; 04-20-2014 at 09:15 PM.
-
-
Legacy Member
can you make a tool like the vickers belt repair tool that looks like pliers. this will give you more control and you can still place the bottom jaw on the vise and hit the top jaw to help get the set pressure
-
Thank You to ActionYobbo For This Useful Post:
-
Contributing Member
Perhaps modify a large pair of vise grips? I could make the tips from a punch or old 3/8 extension maybe and then weld them onto the vise grip. I'll try this first, if it flops that is up next. Thanks!
-
-
-
The Following 2 Members Say Thank You to jmoore For This Useful Post:
-
Ah, flying pig........... You didn't say you were working on steel rivets for a Ross!
-
-
Legacy Member
When rivetting a balance staff, we use two convex punches and a flat one. The two convex punches spread the rivet(two different sized punches). The flat punch flattens it so the hairspring collet lays flat on top of it. Couldn't you do the same thing?
Attachment 52161Attachment 52162
-
-
Contributing Member
Peter, I should have included that in the original post. I knew the Lee-Enfield ones were brass and should have specified what I was working on.
Gsimmons, I think I may wind up having to do something like that. The problem is that the rivets have a nice round head and solid shank. Trying to hold both tools, the guard and spring plus hit the whole works with a hammer is one tough juggle. Was thinking about building the tool with the *** to put in the hole in the mandrel but that's going to be a bit of a fight as well because it has to be a pretty precise affair, the rivet shank is only .092" diameter. Time for more thinking before moving ahead...
Jmoore, your set may be spot on!
-
Thank You to flying pig For This Useful Post:
-
Youir rivet set made me chuckle JM because we had a similar set for rivetting those RIVET, tubular, aircraft on the L1A1 bayonet grips. I don't think ANYONE, ever got it right first or even second time, even with the special mandril seat thing........... We used to call tyhem RIVETS, tubular, awful!
-
Thank You to Peter Laidler For This Useful Post: