-
Contributing Member
Dovetailed fore end splice
Here's the dovetailed fore end splice i've mentioned in another post.
I have a 12x36 Clausing lathe designed for use in both wood and metal. This lathe runs an extremely high spindle speed in wood mode, and cuts like butter with regular wood router bits.
I set the stock up in the milling attachment and align it between centers. Then I mill off the fore end tip nice and square, so the front edge of the splice will be just hidden by the mid band. Then I carefully cut the dovetail. You need to take very precise measurements here, as you want the fore end extension to fit very snugly.

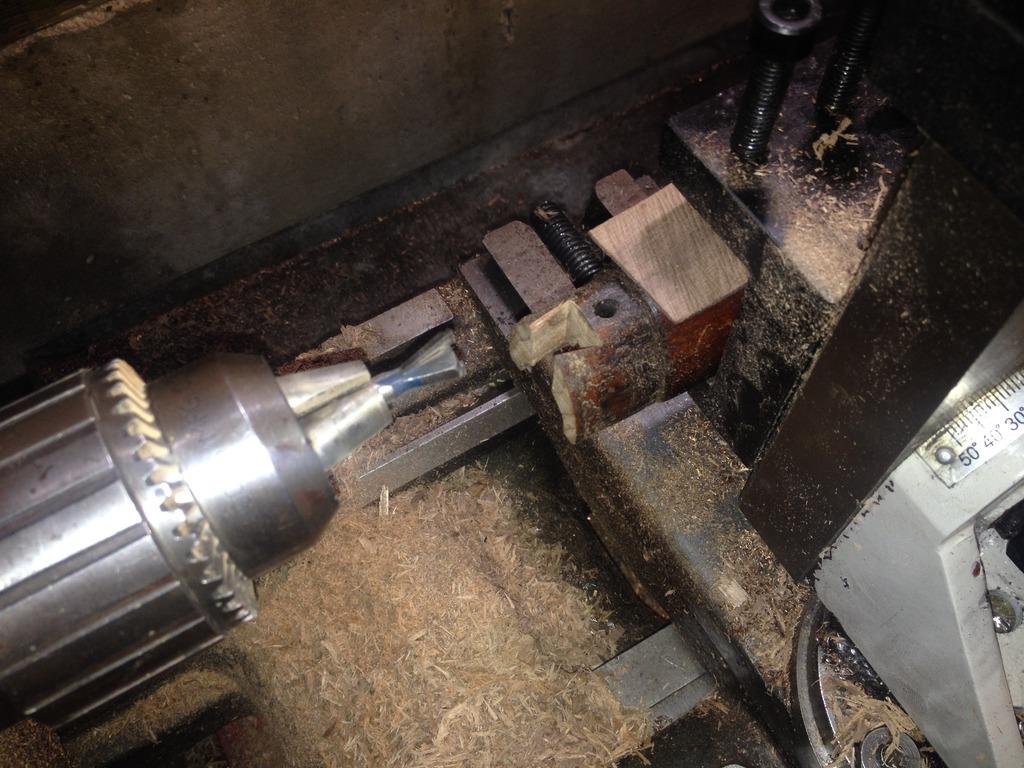
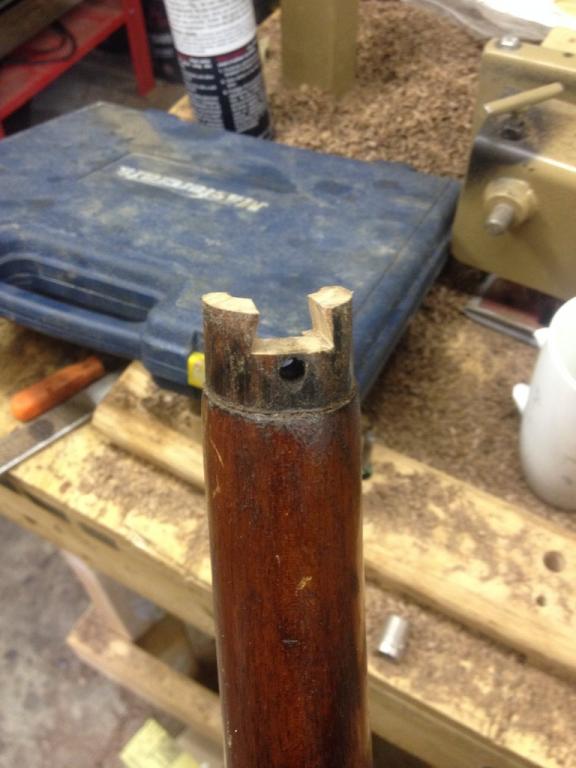
When this is done, you plane one side of your donor fore end. Stick it in the milling attachment with this trued side down. Square it up between centers, then mill the end square. Next you will cut your male dovetail out. Be very careful to not cut it too narrow, you want the fit to be quite snug. It should work out perfectly. Calipers are definitely your friend here...
When this is done, simply glue the new fore end on and let it cure. It will line up perfectly with your choice of square level surfaces. This leaves you with less surfaces to shape.
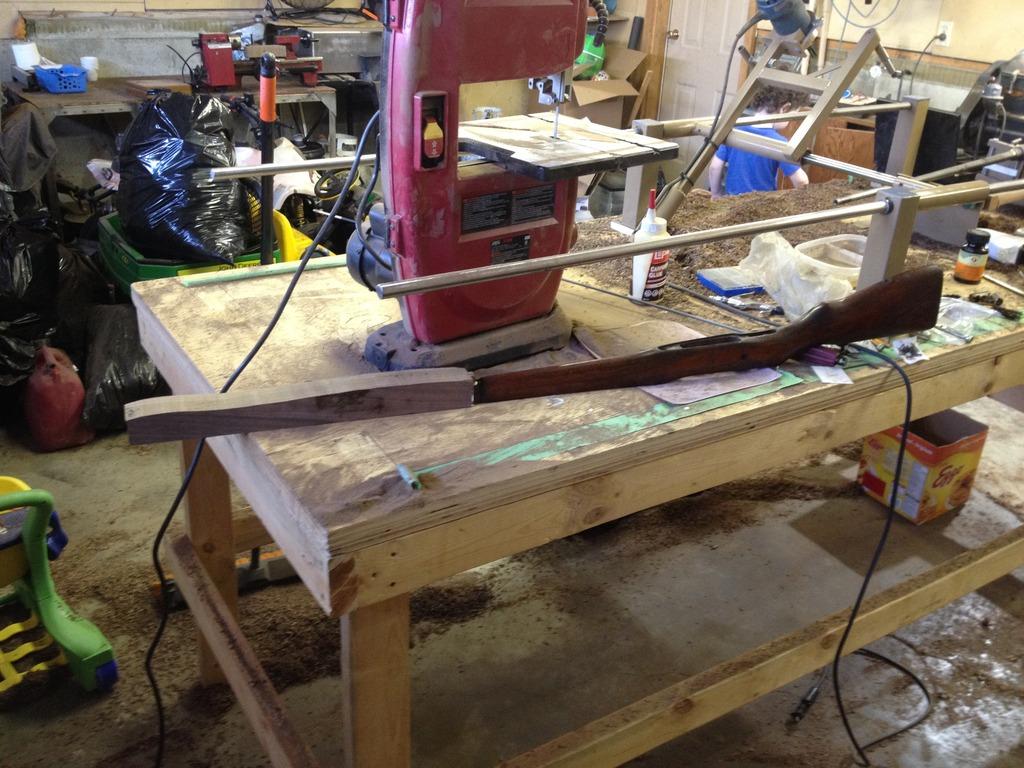
When it is done drying, simply cut your barrel channel as you would to build any other stock. Cut the tip off square to length utilizing the lathe and milling attachment. Cut your intletting so your action beds properly. Then cut the fore end tip to fit the nose cap. Drill for your nose cap screw. Then mill out the tip of the recess for your mid band screw retainer, final sanding, staining and finishing and you are done.
It makes a very strong splice (much much stronger than gluing in dowels with a flush cut) that is still covered by the mid band. This also leaves the straightest possible fore end.
Why would you go to this trouble? Because your barrel moves a lot when being fired, and a doweled splice is not strong. I've heard of several people having theirs break. This is a permanent solution to the problem, and does a much better job in the end.
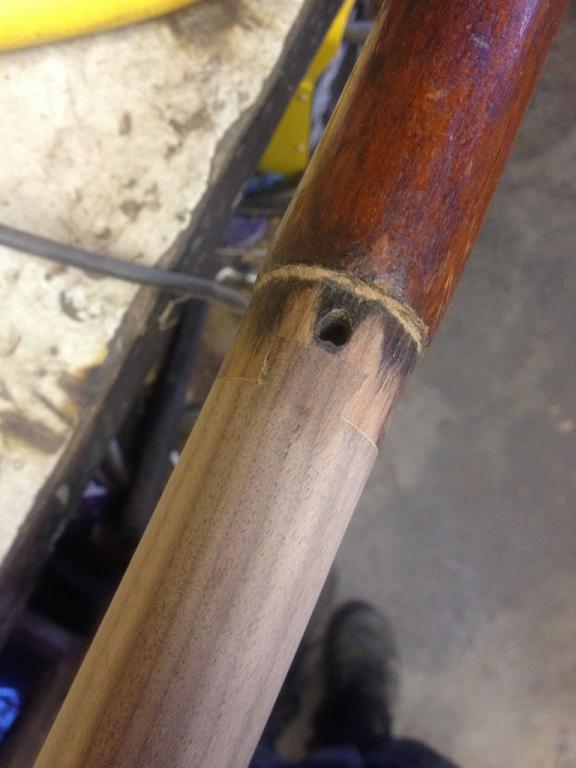
The milling attachment also takes the guess work out of many other repairs. It could also be used to splice and extend butts that have been cut to install rubber butt pads etc.
Information
|
Warning: This is a relatively older thread This discussion is older than 360 days. Some information contained in it may no longer be current. |
|
-
The Following 12 Members Say Thank You to flying pig For This Useful Post:
BrianLara400*,
Bruce_in_Oz,
CINDERS,
Doco overboard,
henry r,
Kiwisteve,
mike1967,
Peter Laidler,
Salt Flat,
Seaspriter,
Vincent,
WarPig1976
-
06-11-2016 07:30 PM
# ADS
Friends and Sponsors
-
Advisory Panel
As always, nice work... Now for Krag
wood...?
-
-
-
Contributing Member
Everything is possible Browning. I'll have more free time in coming months here so the possibility of getting caught up on current orders is there. Stay in touch!
-
Thank You to flying pig For This Useful Post:
-
Legacy Member

Originally Posted by
flying pig
anyone would think you put some serious time and effort into matching the grain. beautiful work.
-
-
Advisory Panel

Originally Posted by
flying pig
Stay in touch!
You can bet the house on it. If you have the time and can manage the production of some of these, you'll sell all you can make.
-
-
Contributing Member
Looking forward to doing something new as well, definitely.
-
The Following 2 Members Say Thank You to flying pig For This Useful Post: